A Shrinking Pie
Salvors face fewer opportunities and mounting challenges.
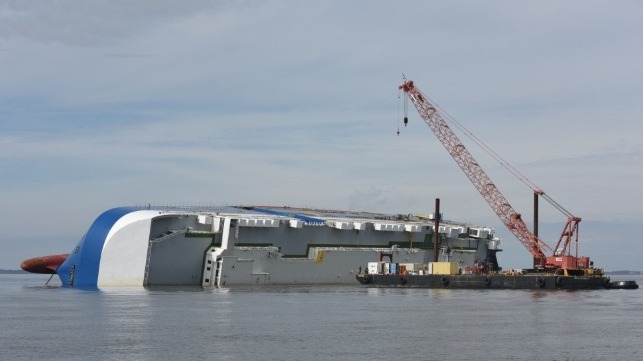
(Article originally published in Sept/Oct 2020 edition.)
The world of marine salvage is changing quickly on multiple fronts. Ships and projects keep getting bigger, but there aren’t as many casualties. There are fewer well-established companies, but there’s a powerful newcomer. Last but not least, the COVID-19 pandemic has added a layer of complexity not only for worker safety but for maintaining the pace of operations as well.
Shutdowns & Quarantines
The COVID-19 shutdown has affected businesses of every kind, especially if they have to move personnel across borders or work in close-quarters environments. Marine salvage has both of these factors, and while projects have continued the experience has been challenging.
In July, the Golden Ray wreck removal in Georgia's St. Simons Sound had to be paused when 10 members of the response crew tested positive for coronavirus. To prevent a recurrence, the T&T-led salvage team has rented out a private resort to house its workers in isolation.
For SMIT, one of the world’s largest commercial salvors, the coronavirus has been both a challenge and an opportunity. When the pandemic began, the company created a COVID-19 management team and a set of strict work protocols and coordinated its rules with subcontractors. This helped speed up deployments. It also turned out to be good for business.
"Early on, we were receiving phone calls from our best clients asking what our COVID-19 protocols were,” says Douglas Martin, President & General Manager of SMIT Salvage Americas. “It was very reassuring to be able to tell them exactly what we were doing. The net result is that our protocols have actually helped us win more contracts. During the COVID period, we’ve worked on the raising of an OSV offshore Fortaleza, Brazil, the grounding of an ultra-large bulk carrier offshore Sao Luis, Brazil, a fire on an amphibious assault ship in San Diego, a grounding and spill involving a bulker near Mauritius and a fire aboard a VLCC offshore Sri Lanka.”
Donjon Marine, SMIT's joint venture partner in the U.S. market, has also invested in COVID-19 prevention. "I firmly believe that to kick this thing and protect the people around us, we have to do some things – not just as a nation, but as a world – that maybe we wouldn't ordinarily want to do," says Executive Vice President John Witte, Jr. "At Donjon we've taken what we believe to be the right precautions to respond to this pandemic, and we've been lucky so far. We've been able to stay viable and keep our people healthy. And that’s really a team effort."
Global salvor Resolve Marine has had considerable success in completing projects despite the challenges of the COVID era. Among other adaptive measures, Resolve’s teams have used teleconferencing for remote consultation.
“In the middle of the pandemic,” notes Dimitris Theodore, Resolve’s Director of Emergency Response, “Resolve responded to a salvage operation in India while the whole country was in one of the most restrictive lockdowns in the world. This was made possible because of Resolve’s local presence in India and collaborative technologies that allowed senior response members in the U.S. and Singapore to consult and interact in real time with teams onsite.”
For Captain V. Seva, head of Singapore-based salvage consultancy VMAX Marine, the COVID-19 shutdown had a personal impact. When he took an overseas salvage job early in the year, he didn’t know that it would take him many months and an ocean crossing to get home again.
"I did a wreck-removal project in the Maldives beginning in February, and at that time none of us understood the magnitude of COVID-19," he states. "When we completed the job there was a lockdown and we couldn’t fly home. Eventually we decided to sail a small dive vessel all the way back to Singapore, crossing the Indian Ocean ahead of monsoon season.”
Sanctions
Lockdowns aren’t the only regulatory hurdle affecting salvage this year. The U.S. Treasury Department has increased its use of sanctions targeting shipping, particularly in pursuit of foreign policy objectives in Iran and Venezuela. In the event of a casualty involving a sanctioned vessel, any salvor has to contemplate whether providing aid could lead to U.S. penalties – and whether it would be possible to accept payment from a sanctioned shipowner.
It’s happened before: U.S. sanctions were an obstacle after the wreck of the Alpine Eternity, a product tanker which allided with an Iranian offshore platform in 2015. Captain Seva was there for the job and remembers the bureaucratic challenge: "The P&I club had to get permission from the U.S. Treasury's Office of Foreign Asset Control, and we had to go through their exemption mechanism in order to manage the casualty."
Now he’s concerned about a much more serious problem. Last year, the Iranian tanker Happiness 1 suffered flooding in her engine room and lost propulsion in the Red Sea. She was carrying one million barrels of oil, and if the situation had deteriorated, a serious spill could have resulted. “No commercial salvor could do anything about it because of the sanctions on Iranian shipping," Seva said.
The vessel was eventually towed into port by Saudi responders, but the outcome could have been different. In January 2018, the Iranian tanker Sanchi burned and sank with all hands off China. If the same incident occurred today, any salvor who assisted her would run the risk of sanctions.
"There must be some form of agreement under which professional salvors are allowed to help a sanctioned vessel quickly because our job is to save lives and protect the environment,” Seva observes. “There must be a line drawn between politics and emergency response."
Supersized Jobs
The size of the salvage market has also changed markedly in recent years. Despite the growth of the world's fleet, the total number of marine casualties has declined and revenue fallen since 2015. The pie is shrinking, but as ships get bigger, so do the jobs.
"Gigantic ships cause gigantic problems," says Nick Haslam, master mariner and special casualty representative (SCR) at consultancy Brookes Bell. "There’s been a significant decline in the number of Lloyds Open Form cases, but I can say from personal experience that the severity of those cases has increased tenfold. We have salvage teams of up to 50 people now and have to mobilize much larger response assets, often from an ocean away."
Container ships, in particular, have undergone a huge growth spurt with the largest now weighing in at 24,000 TEUs in capacity. This has implications for salvors as box ships are susceptible to their own unique marine casualty – the container fire, often sparked by dangerous goods.
Every kind of cargo imaginable ends up on a container ship, and some require special stowage considerations for cooling or ventilation as spelled out in the International Maritime Dangerous Goods Code (IMDG Code). The consequences of getting it wrong are serious: Once reactive chemicals and flammable cargoes catch fire in a box ship's hold, the blaze can be nearly unstoppable.
Part of the risk arises when shippers intentionally misdeclare dangerous goods, but there’s a second component that hasn’t received as much attention: As long as chemical manufacturers are allowed to self-certify their products, dangerous compounds will end up in the wrong place on board.
"The IMDG Code relies on the manufacturer's self-declaration,” says Haslem, “but it's almost impossible to police. What we need is accurate testing and not just 50-gram samples in a laboratory setting. These products are often shipped in bags of up to one cubic meter."
The fate of the 15,000 TEU Maersk Honam is a tragic example of a full-scale container fire. In March 2018, while she was under way off the coast of Oman, the cargo in her forward holds caught fire and burned violently, destroying everything forward of the deckhouse and killing five crewmembers.
According to Haslam, who was appointed by the owners’ P&I club to assist on the salvage, the ship was fully compliant but utterly unprepared for the inferno. Like most container ships, the hatch covers couldn’t be sealed for CO2 flooding, and the crew had only standard firefighting equipment.
New Competition
The salvage market has undergone significant consolidation in recent years, and only a handful of firms with a global footprint and capability remain.
They face a powerful new competitor: China's Ministry of Transport, the parent agency of China Offshore Engineering Solutions (COES) and China Rescue and Salvage Bureau (CRS). In 2015, COES won the contract to raise the wreck of the ferry Sewol – the deepest wreck-raising of its kind – for $73 million. Though it completed the work, it reported that the final cost was roughly twice the bid.
COES also won the contract to remove the wreck of the Kea Trader in 2018 and built a new 800-ton crane barge specifically for the job.
The company advertises an “enviable” ability to offer favorable terms. With the financial backing of the Chinese government, it says it can bid a guaranteed lump sum price at “highly competitive rates” with no extra charge if the project turns out to cost more. And its ambitions extend well beyond salvage: It’s committed to spending nearly $1 billion on a fleet of vessels for offshore construction, heavy lift, dive support, subsea engineering and wind farm installation.
Commercial salvors' views on Chinese competition vary, but many emphasize the importance of experience.
"To the P&I clubs,” says Lindsay Malen-Habib, President of the American Salvage Association and Client Services Manager for Resolve Marine, “it’s appealing to look at a low bid when planning a wreck removal, but it’s also very important to look at the salvor's experience and success rate. Commercial salvors might have a higher up-front cost but may be able to offer more certainty and better protection for the environment."
Paul Benecki is the magazine’s News Editor.
The opinions expressed herein are the author's and not necessarily those of The Maritime Executive.