Could Onboard Carbon Capture Extend the Life of Fossil Bunkers?
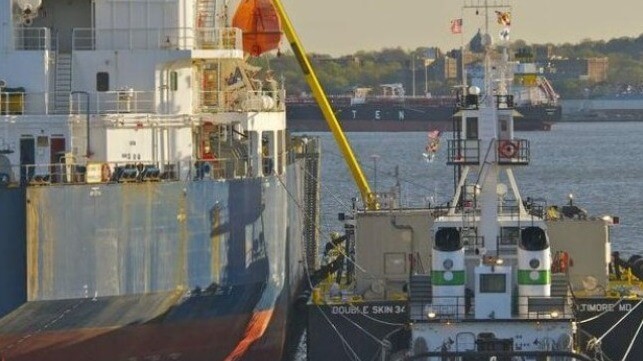
Onboard carbon capture is the only technology that can make conventional marine fuels compatible with emissions goals, and some technologists think it could be a way out of the maritime industry's future-fuel dilemma. Its prospects come down to thorny engineering questions: Will the plant fit on board? Will there be enough space and deadweight to hold the CO2? And where will the captured carbon go when it is offloaded? All will require significant investment and R&D to address.
ABS predicts that investment in onboard carbon capture will increase over the next decade as carbon regulations increase and markets for carbon become more mature, and it has presented a positive outlook for the technology.
"We consider it an interesting solution worth investigation," says Georgios Plevrakis, VP of Global Sustainability at ABS. "It has many challenges with regard to application, optimization, power management and storage. If you look at the most mature technologies now, which are amine-based chemical absorption systems, they take considerable extra power to run. And for every tonne of fuel you consume, you produce three tonnes of CO2 to store, which takes up about three cubic meters of space [if liquefied]."
Given the technical challenges, DNV assesses that onboard carbon capture will have a relatively limited role to play in the green transition. "We try not to rule anything out when it comes to this decarbonization quest, and we do engage in some onboard carbon capture projects," says DNV Maritime CEO Knut Ørbeck-Nilssen. "Personally, I think it makes a lot more sense to try and do [carbon capture] on shore, because you get a different scaling effect and it's easier with the technology to do it at onshore facilities. Whether onboard carbon capture will play a major part I think is doubtful."
Others predict that carbon capture could have practical niche applications in shipboard service. For example, LNG carriers - which run on the boil-off gas from their own cargo tanks - will continue to burn natural gas for the foreseeable future and might benefit from carbon capture, says Rolf Stiefel, Regional Chief Executive for Bureau Veritas M&O. Similarly, short-sea operators who can offload captured carbon frequently - before the weight of the CO2 builds up - might see some benefit.
Onboard carbon capture is also more than just an on/off proposition, and there may be sweet spots where capturing a portion of the CO2 from the exhaust gas helps an existing vessel meet a specific emissions target. Partial emissions capture saves on cost, weight and volume, since the plant required would be smaller.
One other niche application might be particularly practical, according to Torleif Stokke, head of commercialization at Alma Clean Power. Solid oxide fuel cells (SOFCs) can transform natural gas into electrical energy at high efficiency, and the exhaust gas is a high-purity stream of CO2 and water. With relatively little separation, this carbon stream could be captured and stored on board. "The carbon capture discussions are much more relevant when you have a stream of CO2 which is already concentrated," says Stokke.
Work is well under way on developing carbon capture plants for onboard use. Value Maritime already has several reference installations in operation, and multiple major shipyards are designing their own systems, including Samsung Heavy Industries. Qingdao-based scrubber maker Headway has designed a far smaller system for shipboard use, which it believes will make the technology viable for installation. Thanks to a new agitation tank design, the footprint is a fraction of that needed for other alternatives, according to spokesman Mike Zhang.
However the concept of onboard carbon capture looks today, BV's Rolf Stiefel notes that engineering developments can change the prospects of a new technology in unexpected ways. After all, sulfur scrubbers were once widely considered too bulky and impractical to use on ships - before enterprising marine engineers figured out how to make them into a compact, economically-efficient way to keep HFO viable.