Powering Up
Speed, efficiency and reliability characterize the new breed of engines for wind farm support vessels.
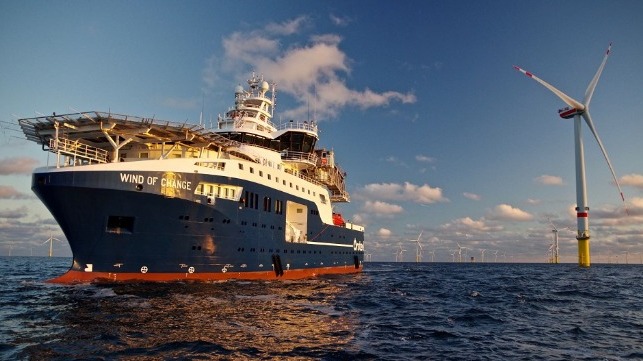
(Article originally published in Nov/Dec 2020 edition.)
The wind farm industry is poised for substantial growth over the next ten years – especially in the U.S. A March 2020 report from the American Wind Farm Association (AWEA) estimates investments of $28 to $57 billion during that period with upwards of 83,000 jobs created. These investments are expected to yield $5.5 to $14.2 billion per year in economic output by 2025, increasing to $12.5 to $25.4 billion by 2030.
Wind lease blocks managed by the Bureau of Ocean Energy Management (BOEM) are in various stages of planning and development off the coasts of California, Hawaii, New York and South Carolina. The New York Bight area alone, extending the length of Long Island, covers over 2,000 nautical square miles and is projected to deliver upwards of 12 gigawatts of offshore wind power in the next decade.
Once constructed, these wind farms will require fleets of specialized support vessels – all of which must be Jones Act-compliant and equipped to transport crews and equipment to the turbine towers offshore. They’ll provide a much-needed boon to U.S. workboat builders, many of whom are still suffering from the OSV glut in the Oil Patch.
Wind farm service operation vessels, or SOVs, are a breed apart. They must be fast, to get the crews out to location quickly. Stable, to support transfers of personnel and cargo. Agile, to safely maneuver within a densely packed field. Powerful, to stay nose-up to the towers in heavy winds and seas. And durable, to stay in the field for days on end, in harsh conditions, with high top speeds and a smooth ride when transiting to and from the turbines.
Service providers want to get their crews out to the towers as quickly as possible since workers’ transit times are “on the clock” and to make sure they’re not seasick and unable to work when they arrive. For guidance on boat designs and operating experience, U.S. naval architects, shipyards and operators are looking to Europe, which has a mature offshore wind industry serviced by hundreds of specialized supply vessels.
Here’s what those solutions look like.
Time-Tested Technology
The solution offered by Volvo Penta is known as the Inboard Performance System or IPS. Introduced to the market over 15 years ago, IPS is a time-tested technology that recently surpassed 30,000 units worldwide.
Unique in design, an IPS installation consists of an azimuthing pod mounted below the hull with twin, counter-rotating propellers mounted to the forward end of the pod for increased efficiency and reduced cavitation. These are coupled directly to the diesel engine, available in power ratings ranging from 300 HP up to 1,000 HP and installed as a complete unit, thereby reducing the installation footprint below decks. Furthermore, IPS units are said to take about 50 percent less time to install versus traditional shaft-based propulsion solutions.
Volvo Penta says the IPS solution delivers 30 to 40 percent longer cruising range, 15 to 20 percent higher top speed, 20 to 35 percent lower fuel consumption, 20 to 30 percent lower CO2 emissions and 50 percent lower perceived noise levels. The pods also produce higher torque and faster acceleration as well as a higher bollard pull of about four tons per unit.
IPS is fully integrated from controls to props and is type-approved by DNV-GL for high-speed and light craft. It’s also capable of dynamic positioning to maintain station automatically.
Looking to the future, Volvo Penta just announced a collaboration with Danfoss Editron to provide a first-of-its-kind hybrid propulsion system for two new wind support vessels being built for Ørsted in the U.K. with deliveries scheduled for mid-2021. The vessels will have four IPS drives, two of which will be driven by Volvo Penta D13 diesels and the other two by Danfoss Editron’s electric motors, powered by a bank of five Volvo Penta D8 variable-speed generators.
This exciting new project will result in the first hybrid-powered crew transfer vessels in the U.K.
Mechanical Advantage
Mitsubishi Turbocharger and Engine America, located in Itasca, Illinois, is responsible for distributing Mitsubishi products throughout the Americas. It has a heavy presence on inland waterways, powering towboats and utilized on tank barges.
Tank barges carrying flammable products require, per USCG regulations, engines that are non-spark, thus limiting the utilization of most new EPA-certified engines that have electronic controls to specially designed barges and locations that keep the engines away from possible fumes. The unique solution that Mitsubishi has brought to the market is mechanically controlled engines manufactured to meet all EPA tiers of emission controls.
All Mitsubishi engines utilize simple mechanical controls and are unique in being able to meet the USCG regulations. Prized for their robust design and simplicity of operation, they help ensure that operators won’t require intervention by a technician should a problem develop. Its newest engine, the EPA Tier 4 S12R-Y4MPTAW-3, is a 49-liter, 1,260-horsepower V-12 operating at 1,600 rpm. With simple mechanical controls and big displacement, it utilizes SCR (selective catalytic reduction) technology to meet NOx Tier 4 emission requirements.
The mechanical advantage is just one of the features that separate Mitsubishi in the propulsion market. Mitsubishi engines are designed for heavy-duty applications and typically offer bigger displacement than those of its competitors. For example, popular 600-horsepower engines average 18 to 19 liters of displacement. Mitsubishi’s 630-horsepower engine has 24.5 liters of displacement, 30 percent bigger and potentially providing longer engine life and reliability.
Mitsubishi engines are popular in the U.S. pilot boat market, and the company is working with local shipbuilders to offer its propulsion solutions specifically for the developing wind farm market.
Walk-to-Work Convenience
When it comes to walk-to-work-designed service operation vessels (SOVs), German propulsion expert SCHOTTEL has been busy providing walk-to-work solutions over the past year.
Taking an approach similar to that installed on offshore oilfield vessels, SCHOTTEL utilizes a diesel-electric system layout on its recent newbuild projects. Typically powered by four diesel generators, the SOVs have different thruster configurations depending on mission requirements. Most, however, run azimuth thrusters astern and bow thrusters forward.
Last year the SOV Wind of Change entered service for the French company Louis Dreyfus Armateurs for long-term charter with Ørsted. The vessel is equipped astern with two azimuthing SCHOTTEL Rudderpropellers, type SRP 430 FP, at 1,660 kW each. Forward are two transverse tunnel thrusters, type STT 6FP, at 1,400 kW each and a SRP 260 R FP Retractable Rudderpropeller. The vessel is also fully DP 2-compliant. a must for performing the walk-to-work operations for which it was designed.
Also launched last year was the Bibby WaveMaster Horizon for operation on the Albatros and Hohe See wind farms in the German North Sea. While designed with a propulsion package similar to Wind of Change, a notable difference is the SRP 260 RT Retractable Rudderpropeller, which can be used as a transverse thruster when retracted. This offers increased flexibility when operating in variable water depths. Like Wind of Change, the vessel is fully DP 2-compliant, allowing for walk-to-work convenience.
The Wind of Hope – sister vessel to Wind of Change – was launched in September of this year and will go on long-term charter to Ørsted as a walk-to-work vessel. While outfitted similarly to Wind of Change, it includes additional operations-support equipment such as a motion-compensated gangway and heave-compensated crane. It will also carry a daughter craft rated for eight personnel and capable of carrying a ton of cargo.
These vessels are designed to serve as long-term accommodation and cargo-support solutions, staying in the field for weeks at a time with a crew of up to 64 service technicians in addition to the regular crew complement. As such, the propulsion systems installed must be powerful and reliable, and SCHOTTEL delivers.
Powerful Solutions for the Modern Wind Farm
While similar in size to oilfield support vessels, the design and mission intent of these new-generation SOVs could not be more different. Unique in their speed and comfort requirements, they require robust propulsion systems that offer leading reliability, power and efficiency to perform in the challenging environments that characterize offshore wind farms.
Whether providing single components or a full turnkey solution, these companies are both mature in the international market and moving to the forefront of the burgeoning U.S. wind farm market. By providing world-class equipment and service, they enable vessel operators to perform with confidence in the most challenging of conditions.
Sean Hogue is a Master Mariner and Vice President of Marine Assurance at Baker Marine Solutions.
The opinions expressed herein are the author's and not necessarily those of The Maritime Executive.