Supporting Shipping’s Transition Towards a Carbon-Free Future
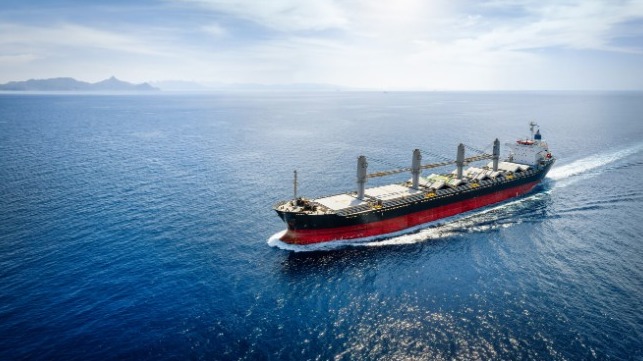
Dr Olivier Denizart, Technical Manager at Lubmarine, shares some of the key findings on Lubmarine’s latest R&D projects on future fuels including experiments on an ammonia-fueled engine that it has modified – and the critical importance that safety will have to play in shaping the implementation of new fuels.
The last 18 months has seen the global shipping industry really start to accelerate its decarbonization journey.
LNG is now recognized as a mature and best immediate option to help reduce shipping’s CO2 emissions today, whilst at the same time providing the technological platform for the transition to new fuels including biofuels, ammonia and methanol.
As the speed of new fuel development ramps up, the challenge for lubricant manufacturers is to stay ahead of those changes to ensure that, when those fuels do become commercially viable, we have lubricant solutions available that are tried, tested and ready to support our customers as we evolve towards a carbon-free future.
From its inception over 70 years ago, Lubmarine has always embraced a pioneer spirit to develop and deliver market-leading marine lubricants. And as we enter this multi-fuel future, this ethos remains at the forefront of our development – with a significant investment in our own R&D and a willing and active commitment to cross-industry collaboration.
Along with Methanol, Ammonia has been recognized as a viable fuel solution, one that, whilst offering opportunities towards GHG reduction targets, also poses key challenges from the perspectives of safety (both environmental and human) and practicality. Providing good combustion in a dual fuel engine, another advantage to shipping is that ammonia should face less competition with other areas of the transport sector – unlike some of the other fuel alternatives being considered.
Ammonia storage already exists in 120 ports globally, enabling both ship-to-shore and ship-to-ship bunkering solutions alongside reasonable liquefaction temperatures. But it is far from plain sailing when it comes to ammonia with significant challenges around its volumetric energy density and of course its deadly toxicity and the need for stringent safety solutions.
At the same time OEMs are developing NH3 engines with MAN ES and WinGD anticipating it will launch a two-stroke ammonia-fueled engine in 2024.
It’s a fuel solution we are actively researching here at Lubmarine, with our R&D teams having redesigned a 1.5-liter passenger car diesel engine to run on ammonia. This enables us to run our own in-house tests to better understand the impact that ammonia will have on engines - and specifically for us, the impact and challenges for effective engine lubrication.
With any new fuel, we must understand the interactions and impacts of the relationship between lubricant, fuel, and engine to ensure that our lubricants are delivering the desired performance and, through lifecycle assessments, be assured that there will be no carbon generation.
It’s a methodology that starts in our labs with our ammonia engine oil development project.
Our Test Approach
From an initial perspective, we wanted to show that NH3 can interact with lubricant chemistry so our challenge is to fully understand its operating behaviors to enable us to adapt lubricant formulations to meet specific needs.
When it comes to lab testing, our key objective is to develop an engine oil technology that allows reliable, clean, and efficient use in Ammonia-fuelled internal combustion engines.
To meet these objectives, we need to:
- Observe - lubrification challenges in a real engine environment - deposits, wear, corrosion, oil ageing.
- Evaluate - sensitivity to engine oil composition.
- Calibrate - laboratory test severity.
Our challenge is to understand the impact that NH3 has on oil components and their performances, the availability of NH3 ICE tests (performance, endurance), access to large engine prototypes and our need to run and understand evaluation test results.
Key observation and assessment areas when we are running ammonia engine tests include:
- Ammonia dilution
- Nitro-oxidation
- Corrosion
- Cylinder wall degreasing
- Water handling
- Deposit control
- Material/Elastomer compatibility
Testing protocols look at three specific areas:
- Oil formulation – including base oils and additives.
- NH3 Alteration Tests –influence of temperature and crankcase gases composition.
- Performance evaluation
2024 will be a very key year for us here at Lubmarine with regarding to lubrication development to reflect new fuels.
Thanks to our R&D and OEM‘s partnership we’ll start lubricating tug boats using an ammonia-fuelled 4-stroke engine this year.
On the methanol side, we are starting trails with methanol 2-stroke commercial engines.
From our lab test results to date we have been able to analyse the oxidation and main characteristics of our lubricants where they have been adapted to methanol-fuelled engines.
What we have been able to do is widen our testing to incorporate actual field tests on these new engines which is providing invaluable data from which we are able to evaluate, implement and apply to further tests to support product development.
Dr Olivier Denizart is Technical Manager at Lubmarine.
The opinions expressed herein are the author's and not necessarily those of The Maritime Executive.