Shell Joins 3D Printing Project for Repair of Undersea Pipelines
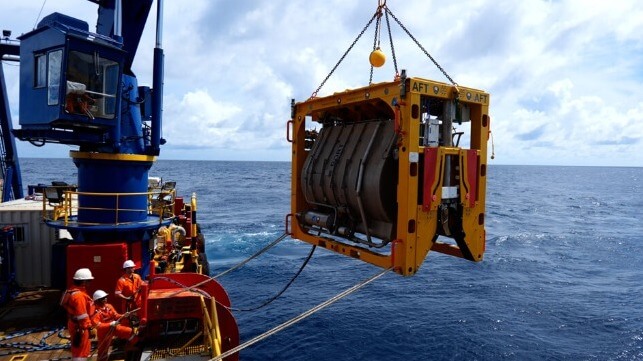
Shell is joining a joint industry project that is working to develop and test advanced 3D printing technologies to be used for ocean repairs of undersea assets. According to the partners in the project, it will be a “game-changing way of conducting subsea repairs,” with the potential to extend the lifetime of existing and future underwater assets. The project has achieved important milestones and expects to deploy by 2024.
The project was launched in 2021, led by Kongsberg Ferrotech, a Norwegian company that offers robotic services for inspection, repair, and maintenance of underwater installations across the energy and maritime sector, along with Equinor, Gassco, and SINTEF. The joint industry collaboration is supported by the Research Council of Norway. The companies said that they believe combining 3D printing with Kongsberg Ferrotech’s robot will open new possibilities for subsea repairs and modifications.
“When we discovered this joint industry project, we realized that the repair methods have many applications within Shell’s global operations,” said Angeline Goh, 3D Printing Technology Manager for Shell. “The technology is of great interest to Shell and fits nicely into our portfolio of advanced technology for subsea robotics and 3D printing.”
The project is developing advanced 3D printing technologies for metal-to-metal repairs of underwater assets. They highlight that additive manufacturing (3D printing) is expected to have great financial and environmental benefits for installed as well as future subsea assets. 3D printing also meets the main criteria for sustainability, to reduce, reuse, and recycle.
In the repair process, a dry environment is created to offer high-quality repairs without disrupting ongoing operations. The technology is designed to conduct repairs and modifications of underwater assets including those used by the oil and gas industry, hydrogen transmission grids, wind farms, or transmission cables.
The project has identified several applications such as the repair of cracks, dents, and the replacement of lost materials where the technology will be very beneficial compared to traditional methods. The project is currently in the process of qualifying the 3D printing technology for cracks and dents.
3D printing technology under development to repair subsea assets in place (Kongsberg Ferrortech)
“Together with our partners we’re now preparing for the world’s first test of 3D printing repairs in demanding ocean spaces,” says Torgeir Bræin, CTO at Kongsberg Ferrotech. “With another global partner onboard, we’re able to adapt our technology towards a large global market.”
Kongsberg Ferrotech will integrate 3D printing technology with its Inspection, Repair, and Maintenance (IMR) robots. The company working with Rovula, a platform for subsea inspections, recently carried out the world’s first robotic composite repair on a producing subsea pipeline. The robot, called Nautilus, was deployed near Bangkok of a pipeline operated by Thailand’s national natural gas transmission company PTTEP.
Nautilus is equipped with various inspection and repair tools which makes it possible to conduct an inspection, repair, and maintenance without remotely operated vehicles, divers, and other vessel-supported equipment. Kongsberg Ferrotech reports in a single dive the system can remove existing corrosion coating, conduct defect sizing, surface preparation, coating, leak sealing, and structural strengthening using carbon fiber.
Traditionally, skilled divers must board a pressurized submarine diving deep under the sea to perform these tasks. The partners also said that the robot also reduces the possibility of mistakes that can cause accidents or cracks and damage to a pipeline.