How Much Could Carbon Capture Help Shipowners Meet CO2 Targets?
Within a few years, new multipollutant scrubbers may significantly reduce GHG emissions from existing ships
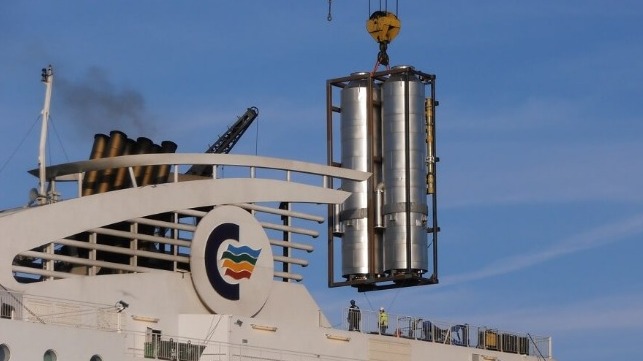
As the maritime industry looks for practical ways to reduce greenhouse gas emissions to meet long-term climate goals, it is also turning attention to technologies that can start cutting down on carbon right away. Carbon capture is one possibility, and several suppliers are working on systems that can scrub CO2 - and other pollutants - out of the exhaust stream of existing ships. Technology company Wärtsilä is a leading maker of SOx scrubbers, and it is leveraging its experience in order to develop new multipollutant scrubber systems.
To learn more, TME caught up with Kashif Javaid, Director of Sales for Wärtsilä Exhaust Treatment, to get the details on technology that could bring down the emissions of today's conventionally-fueled merchant fleet.
TME: Broadly, what kind of potential do marine scrubbers have for removing pollutants beyond SOx (PM, NOx, CO2, etc.)?
With mounting regulatory and social pressure to reduce Greenhouse Gas emissions in shipping, we believe that it’s sensible to take a holistic approach in view of the scale of the challenge. The first step is realizing the scale of the impact we are having beyond just focusing on CO2.
Currently, the shipping industry is responsible for 15 percent of the world’s NOx emissions, 14 percent of the world’s SOx emissions, 2.5 percent of the world’s CO2 emissions - and a significant share of the world’s particulate matter (PM) emissions.
With this range of pollutants in mind, it’s only right that Wärtsilä Exhaust Treatment works to develop modular, lifecycle technologies that can tackle this full scope.
We have always taken the view that scrubbers can provide the industry with a springboard that can be built upon, with SOx scrubbing acting as merely the starting point for us to grapple with the maritime sustainability challenge. Alongside SOx, we brought to market selective catalytic reduction systems (SCR) and Exhaust Gas Recirculation (EGR) to reduce NOx emissions, and we are now adding PM filters. Excitingly, and as we have announced last year, we are also working on tackling CO2 directly through carbon capture and storage, capitalizing on the knowledge gained from bringing SOx scrubbers to market.
As with all our abatement technologies, they are built with modularity and flexibility in mind, and can be applied to a variety of vessels. Our approach not only demonstrates our commitment to constantly improving scrubbing technology, but also how technology can effectively futureproof shipping assets against future sustainability challenges.
TME: For CO2 removal, what percentage of emissions can be extracted from the exhaust stream, within limits of practicality and cost?
Carbon capture is exciting because it can provide significant reductions in a relatively short timeframe. We are developing our Carbon Capture and Storage (CCS) solution in line with the IMO’s targets, with the aim of reducing up to 70 percent of CO2 emissions per vessel.
The system relies on a dedicated solvent, and would therefore require a separate CO2 removal stage, but it may be possible to integrate this stage into a conventional scrubber. It will also offer different degrees of carbon treatment, and once captured will be stored in tanks for delivery to carbon storage facilities on land.
TME: What are the best CO2 storage solutions available, and how do they impact the vessel's capacity?
The CO2 captured will be stored on tanks and off-loaded at port reception facilities. Currently permanent sequestration options are mostly in Northern Europe, with more emerging in North America, where the CO2 is pumped into used oil fields. However, we are certain that more infrastructure will follow as the world rallies around the potential transformative impact of CCS on the global fight to decarbonize.
CO2 storage on board would have a space implication. Part of our R&D process at the minute is to establish the capacity that would be taken up by a CCS system and factor this into the use case for owners and operators.
We are excited by what the development of our CCS solution could mean for the industry, particularly with respect to maintaining the profitability of existing assets, effectively safeguarding them into the future.
TME: What kinds of scrubber technologies look best to Wärtsilä for this purpose?
It is less about scrubber technologies and more about the capture techniques that we are looking to deploy. Currently, we’re exploring a solvent-based option, as this is based on already established research and development in solvents, and this huge backdrop of chemistry from other industries.
This method uses either a liquid solvent (or solid sorbent) to absorb CO2 from the exhaust gas, and then uses pressure and/or temperature to release the CO2 from the solvent or sorbent.
There are hundreds of solvents available, many of which are being used in land-based systems already. We will be testing solvents this year to explore the best options for ship application.
Two of the main technical qualities we’re looking for in solvents is their lifetime and the heat demand associated with stripping the CO2. Different solvents require different temperatures, which also leads to cost implications. Our goal is to find a solvent that operates at a lower temperature so that the heat demand is lower.
TME: And what are the waste management requirements for their operation?
In most cases, removing PM upstream of the CCS plant will be required. This has the double benefit of prolonging the lifetime of the solvent, as well as almost eliminating the PM emissions from the vessel. This does also create a small waste stream for the captured soot and particulates, but it can be handled by our existing open-loop washwater treatment. Additionally, the solvent will need to be replaced and/or regenerated at regular intervals.
TME: How do multi-pollutant scrubbers look commercially? Are the costs offset by the ability to use low-cost fuel like HFO?
From conversations we’ve had with customers and partners, there is huge appetite for technologies that have the ability to work together around the stack to reduce multiple pollutants.
What’s clear is that shipping needs to demonstrate some action now on decarbonization. In the absence of any single solution, following multiple pathways is the right thing to do. A meaningful amount of shipping’s global fleet could embrace the abatement technologies produced by Wärtsilä Exhaust Treatment to drive a noticeable impact.
We believe that scrubbers are an excellent platform for us to build further upon, creating new technologies that work together in the stack and across the propulsion chain to tackle a range of different emitted substances. The wider expertise of Wärtsilä, particularly in engines and other marine solutions, will allow us to build a holistic offering that strives to improve maritime sustainability.
Indeed, the fuel spread between HSFO and VLSFO cements scrubbers’ competitive role as a solution to tackle shipping’s sustainability challenges. Current prices continue to favor scrubbers as the compliance option for the Sulphur Cap regulations brought into effect in 2020, but what scrubbers also enable is entry to further abatement.
TME: When might we expect this technology to come to market at scale?
We have now installed a 1MW pilot plant at our test facility in Moss, Norway to test our CCS technologies in a range of scenarios and conditions. We are already making strong progress, with initial tests of the system already proving that it meets our ambition of capturing 70 percent of CO2 at the point of exhaust. Most importantly we’re using this system to identify the unique particularities of designing a CCS system for ships, and to find ways to maintain health and safety of crew and assets.
One of the next key steps for us is to undertake a pilot retrofit installation of our CCS technology on Solvang’s 20,000-dwt ethylene carrier Clipper Eos by 2023. This demonstrates to the industry that we are only a few years away from bringing to market another viable pathway to shipping’s decarbonization journey.