From Keels to Coatings and Beyond
The role of the modern shipyard is multifaceted and constantly evolving
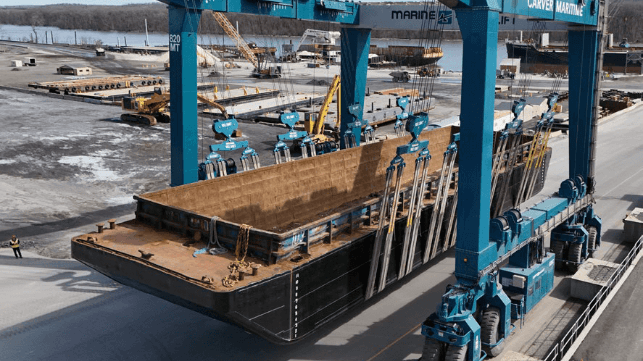
(Article originally published in May/June 2025 edition.)
According to a recent report from UNCTAD, global maritime trade is projected to grow an average of nearly three percent a year through 2029.
The shipbuilding and repair market is projected to grow even faster, from $260 billion in 2024 to $279 billion in 2025 or just over seven percent. This growth can be attributed to rising population, economic expansion in emerging markets and increasing demand for all things – 80 percent of which are carried by sea.
Commercial vessels must be drydocked once every five years while passenger vessels need to go twice in that same period (with a maximum interval of 36 months between overhauls), thereby providing a steady flow of business to repair yards.
Considering growth in the global cruise market, which is projected to increase by 26 percent by 2029 to $53.5 billion in revenue, and you can see that drydock space will come at a premium.
More ships, more shipping, more shipyards.
MODERN SHIPYARD OPERATIONS
To win the work, yards must stay competitive. Modern facilities, larger docks and faster turnaround times are all key considerations in selecting a yard.
This type of forward planning and progressive practice is exemplified at BLRT Repair Yards, based in Tallinn, Estonia with additional yards in Lithuania, Finland and Norway. Boasting the largest floating dock in the Baltics and one of the largest in Northern Europe, and a total of seven docks across all locations, BLRT has the capacity required.
"What sets us apart is our ability to combine craftsmanship, modern technology and forward-thinking project management," says BLRT CEO Andrejus Babachinas.
Technology such as robotic welding, automated surface preparation and AI-assisted inspection technologies where feasible give the company an edge. Using digital twin and predictive maintenance techniques, the company is able to better optimize planning and operations with the ultimate goal of shifting to a proactive maintenance approach.
The use of energy-efficient coatings and application technology, installation of hybrid propulsion systems and recommendations for improved hydrodynamics work hand-in-hand with clients sustainability and environmental goals.
"At BLRT Repair Yards, we believe that maintaining a vessel's reliability and extending its life is more than just a service – it's a partnership," Babachinas says. "Every ship we work on represents a commitment to safety, efficiency and sustainability. We see it as breathing new life into vessels, ensuring they are stronger, safer and ready for the seas ahead."
SUPPORTING THE GREAT LAKES
An important sector of the U.S. market is the Great Lakes fleet.
The five Great Lakes, their connecting channels and the St. Lawrence River form one of the longest deep draft navigation systems in the world – the St. Lawrence Seaway. Moving over 32 million metric tons of cargo each year, the Seaway plays a vital role in North American shipping.
Located on the shores of Erie, Pennsylvania, on the site of the former Bethlehem Steel Shipyard, Donjon Shipbuilding & Repair operates the largest shipyard of its kind on the Great Lakes.
Equipped with a 1,250 foot drydock, it's one of only two drydocks on the Great Lakes capable of handling 1,000-foot Great Lakes Self-Unloading vessels, giving it a unique capacity to build, repair, refit and re-power ships.
Located on 44 acres, the Erie facility has more than 200,000 square feet of production area, including fully enclosed fabrication and assembly buildings, as well as 4,000 feet of pier space.
From its beginnings in 1964 as a marine salvage provider, Donjon has continued a measured expansion over time into dredging, decommissioning and recycling, and heavylift support services.
This integrated skill set allows Donjon to add value to any number of operations including the response to the Francis Scott Key bridge removal following its collapse after being struck by the containership Dali in March 2024. The company was able to respond with almost all of its substantial fleet, led by the 1,000-ton capacity derrick barge, Chesapeake 1000.
MAINTAINING MILITARY MIGHT
Since its inception in 1917, the shipyard facility located offshore Mobile, Alabama, on Pinto Island – now home to Alabama Shipyard (ASY) – has played a vital role in serving the U.S. Navy.
During World War II, it produced twenty Liberty Ships in support of the war effort and over 100 T2 tankers – known as "navy oilers" – used to transport fuel oil, diesel fuel, gasoline and sometimes black crude. Many of these ships returned for years afterwards as the yard provided ongoing maintenance and repair support.
That legacy of support and service continues today with a fresh restructuring aimed at partnering more closely with the U.S. Navy while taking advantage of progressive new American shipbuilding initiatives.
Backed by the private equity-supported United Submarine Alliance Qualified Opportunity Fund (USA Fund), the land upon which ASY sits was sold to the newly created Mobile Naval Yard, LLC. ASY subsequently leased back 70 acres of the original 356-acre site, resulting in a right-sized footprint for its operations.
Additional capital will be invested in infrastructure upgrades and improvements across the whole site, allowing for enhanced support of the Maritime Industrial Base (MIB). These improvements will enhance the yards' capabilities, allowing ASY and other future tenants to more effectively support the MIB and contribute to the restoration of America's shipbuilding and repair capacity.
MULTIPURPOSE FACILITY
The Port of Coeymans, located south of Albany on the Hudson River, is New York's premier industrial waterfront terminal.
Owned and operated privately by Carver Companies, the owner and staff are dedicated to providing customers with top-flight service from a prime location for all shipping, processing, warehousing and transportation needs.
Capable of handling vessels up to 750 feet in length, the dock is heavylift-rated up to 4,000 pounds per square foot. This allows the terminal to undertake a variety of projects as the site is equipped to handle modularization of power plants and bridges as well as small manufacturing, marine construction, aggregates and disaster-recovery projects.
Strategically located at the port, Carver Companies offers comprehensive vessel repair, maintenance and fabrication services inclusive of tugboats, barges, offshore supply vessels and much more. The facility features a Marine Travelift capable of hauling vessels up to 820 metric tons and 60 feet in beam for drydock and topside repair services. With more than two acres of outdoor storage and an indoor bay spanning 100'x300'x88', projects are ensured to stay on track regardless of weather conditions.
Who says shipyards are just for ships?
MULTI-CAPABLE YARD
Shipyards are land- and resource-intensive, requiring dock space, drydocks, travel lifts, heavy equipment and workshops. If you find yourself sailing in the Caribbean, then Astivik Shipyard has these resources at the ready.
With facilities spread over seven hectares, it's equipped with three floating drydocks, a 220-ton slipway drydock with three docking positions (one of which specially equipped with airbags for barges), more than 300 meters of pier for alongside works, rolling equipment such as cranes, forklifts and telehandlers plus 2,155 square meters of covered workshops.
Founded in 1972 in Cartagena, Colombia, Astivik has evolved into one of the leading shipyards in the Caribbean. Key milestones include expanding into construction and maintenance for the national market in the 1980s, launching Colombia's first domestically designed floating dock in 2004 and increasing lifting capacity to 4,000 tons by 2011 with the addition of multiple docks.
In 2016, the strategy shifted toward the export of services, and by 2024 nearly 80 percent of revenue came from international clients.
Thanks to an exemption under the Jones Act, U.S.-flagged vessels can receive repair and maintenance services in Cartagena without incurring any taxes upon returning to the U.S. This makes Astivik and Cartagena a strategic and cost-effective choice.
With over 50 years in operation, the yard stands proud as a premier facility in the Caribbean.
SHIPPING'S SUPPORT STRUCTURES
Ship repair yards play a crucial role in maintaining and modernizing the global fleet of ships. They're shipping's support structures, providing essential maintenance, repair and alteration services for a wide range of vessels, ensuring they remain operational and compliant with regulations.
With an ever-expanding fleet, modernization is the name of the game. Yards are adapting to become bigger, faster and more efficient by adopting the latest technologies to shorten stays and increase regulatory compliance.
Modern vessel owners require their vendors to handle increasingly sophisticated ships and equipment, moving them through quickly while being stewards of the environment. Modern shipyards are rising to the challenge, offering full support from keels to coatings and beyond.
Master mariner SEAN HOGUE is a frequent contributor to The Maritime Executive.
The opinions expressed herein are the author's and not necessarily those of The Maritime Executive.