Techno-Pilgrims
The Mayflower sails again!
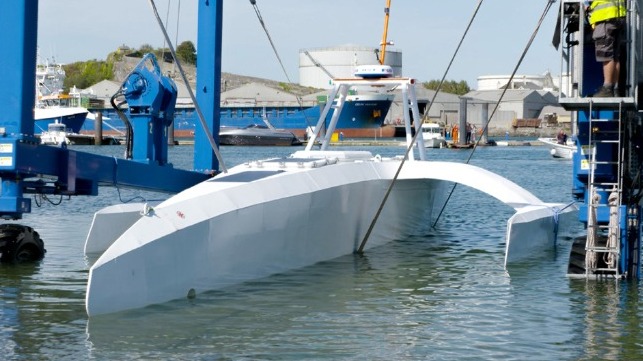
(Article originally published in July/Aug 2020 edition.)
The year was 1620 when 135 English Puritans, known today as the Pilgrims, decided to brave the treacherous open seas in search of religious freedom in a new promised land. Nearly 400 years ago to the month, the Mayflower departed Plymouth, England for a grueling, 10-week Atlantic crossing on her way to the New World – a voyage that changed the course of history.
Four centuries later – and perhaps at the pinnacle of human innovation – the world’s first full-sized autonomous vessel looks to honor those that risked it all for a better future. At 15 meters (49 feet) and five tons, the Mayflower Autonomous Ship (MAS) – a collaboration among the non-profit ProMare, IBM and Wärtsilä – will replicate the original Mayflower’s voyage later this year. The unmanned, autonomous vessel will self-navigate from Plymouth, England to Plymouth, Massachusetts utilizing renewable energy, artificial intelligence and enhanced sensors to further unlock the mysteries of the ocean, autonomy and renewable energy.
The Mayflower will once again alter the course of history.
Evolution
With varying degrees of autonomy – ranging from automated onboard support for seafarers to completely unmanned – the global autonomous vessel industry is rapidly evolving. Report Linker expects the market for such vessels to grow from $13.2 billion in 2019 to $21.7 billion by the end of 2025, even accounting for COVID-19, as more players enter the market. Nonetheless, perhaps the two most pressing questions are (a) why is there a need for autonomous vessels, and (b) how soon till they are ready for primetime?
The answer to the first may seem obvious. From a commercial perspective, the increased safety achieved by reducing operator load and decision fatigue by delegating functions like cycling mechanical pumps, weather reporting and even navigation to a computer has been clearly demonstrated. According to the U.S. Coast Guard and the National Transportation Safety Board, crew fatigue, inadequate training and human error contribute to 96 percent of all maritime incidents, which makes “automation” music to the ears of insurance firms.
Finding talented crew is another concern. MARAD has stated the need for 70,000 new seafarers by 2022 and BIMCO, the largest of the international shipping associations, predicts a global shortage of 147,500 skilled maritime workers by 2025. The workforce is aging with little desire among young people to go into the industry.
From a national security perspective, the U.S. Navy has suffered for 19 straight years from an overextended fleet that has shrunk by 20 percent while the number of deployments has remained the same. A continually evolving threat matrix and shrinking resources make it difficult to maintain combat credibility as a global power in anti-access/area denial operations.
For context, former Chief of Naval Operations Admiral John Richardson warned in 2018 that the Navy is observing “increasingly regular deployments of Chinese ships in the North Atlantic and Russian underwater-fleet activity that hasn’t been witnessed for the past quarter-century.” To keep pace, the Navy is integrating autonomous vessels into its operations to provide enhanced domain awareness and operational presence while reducing the possibility of detection.
The use of autonomous vessels will also deter, detect and counter threats, improve search and rescue, prevent illegal fishing, stop intrusions into protected marine sanctuaries and identify and respond to oil-spill incidents. Compared to operating a typical Navy destroyer at $700,000 per day, the Defense Advanced Research Projects Agency’s Medium Displacement Unmanned Surface Vessel – the successfully demonstrated Sea Hunter – only requires $15,000/$20,000 per day. For the cost of one Littoral Combat Ship, the Navy could deploy an entire fleet of autonomous surface vessels (ASVs).
As to how soon ASVs will be ready for prime time, IMO’s Maritime Safety Committee (MSC) is expected to finish its regulatory “scoping exercise” (used to determine the legal framework for items like navigation and safe manning) this year. In the meantime, 2019’s 101st MSC session approved Interim Guidelines for Maritime Autonomous Surface Ships (MASS) trials.
Nonetheless, when asked the same question, Thomas Pedersen, Director of Automation & Dynamic Positioning Systems at Wärtsilä Voyage Solutions, replied, “Now!”
Trialing the Smart Ship
Well-known for its marine propulsion systems, Wärtsilä has been transitioning from an equipment maker to a “smart marine” technology company. As part of the transition, it’s acquired L3-Maritime Systems, Eniram, Guidance Marine, MSI and Transas along with establishing the Wärtsilä Acceleration Center in Singapore to promote innovation by collaborating with industry, academia and local partners – one of three such centers worldwide.
Wärtsilä recently completed a 365-day trial in Singapore with its IntelliTug, the first commercial MASS system to demonstrate its Smart Navigation System (SNS). SNS includes passage planning with collision avoidance, virtual anchoring with guard circle, adaptive speed, parking assistance and enhanced situational awareness. Used on the IntelliTug and integrated with IBM’s “AI Captain” technology aboard the Mayflower, Wärtsilä’s near-field RS24 offers high-speed, high-definition K-band radar with greater resolution and fewer blind spots than S- or X-band – essential for close-quarters maneuvering and automatic dynamic route-planning for collision avoidance.
Since 2015 Wärtsilä has gained significant competencies by operating a remotely controlled vessel in Aberdeen, U.K. via SATCOMs from San Diego, California. Pedersen explains that, instead of taking “moonshots,” a step-by-step, evidence-driven and user-centric design approach is best practice. Wärtsilä’s Smart Maneuvering Suite is solving autonomous “undocking – transit – docking” to achieve reduced maneuvering times and lower fuel consumption through uniform execution and optimized performance.
Separately, Boston-based Sea Machines Robotics is trialing the SM360 AI-powered dynamic obstacle avoidance (with target tracking/identification and course prediction) aboard an AP Moeller-Maersk Ice-Class container vessel. By providing advanced situational awareness for piloting including the use of thermal screens throughout the wheelhouse fed from integrated sensor data, a full panoramic picture alleviates blind spots and poor visibility. The goal? Reduce the risk of unexpected incidents, accidents and delays that impact cargo schedules and bottom lines. The SM360 is expected to become commercially available this year.
In 2019, Sea Machines partnered with the Marine Spill Response Corporation (MSRC) to demonstrate the effectiveness of autonomous vessel operation in oil-spill response situations for MARAD. Following the event, Deputy Maritime Administrator Richard Balzano stated, “Response timing is critical. The sooner we can get to a spill, the sooner we can control it and the less damage it can do. Remote systems, as demonstrated, can be more effective and respond quicker. If this industry is going to be competitive and safer and evolve, it has to look at remote technologies.”
The Mayflower’s Brains
Looking to unlock the secrets of the ocean, 95 percent of which remains unexplored, the U.S. nonprofit marine research and exploration firm ProMare has partnered with IBM’s artificial intelligence (AI), cloud and edge technologies to create AI Captain, the “brains” of the Mayflower Autonomous Ship (MAS). With help from the University of Plymouth, the MAS aluminum-hull trimaran will not only replicate the original Mayflower’s voyage but also study plastics pollution and its effects on the ocean.
“It’s all about top-to-bottom research,” says Brett Phaneuf, Founding Board Member of ProMare. “The very interesting part is the AI side. Integrated weather sensors with IBM technology look at all parameters of the environment and its own self. The system goes about its business and is able to detect and react to dynamic situations such as buoys, debris and ships. It will even stop and think, ‘This is odd. Maybe the humans would be interested in knowing.’ The entire design was driven by, and for, AI.”
Phaneuf believes the project will advance autonomous technology by leaps and bounds and yield massive commercial and scientific benefits.
Remote Inspection Technologies
Complementing the disruption created by unmanned vessels are changes to maritime inspections and surveys. Class societies may soon find their ranks of surveyors diminished as new Remote Inspection Technologies (RITs) are integrated.
As evidence, ABS has published its Guidance Notes on the Use of Remote Inspection Technologies. In line with the International Association of Classification Societies (IACS) guidelines for RITs, their adoption reduces safety risks to surveyors (e.g., working at heights or in confined spaces), provides a benefit to the owner/operator by reducing operational intrusiveness and unlocks new layers of value via “digital data” from live video, 360° virtual tours, LiDAR, digital asset twins and, yes, blockchain.
Despite the catalog of challenges remaining to be solved by unmanned and autonomous vessels – such as onboard critical equipment failures, damages at sea and minimum manning requirements – the sun is rising on this technology. Just as our ancestors did 400 years ago, today’s techno-Pilgrims are helping make way for a safer, cleaner and more independent future for generations to come.
Sean Holt is a regular contributor and co-founder/CEO of the startup Quantum Dynamics, which is focused on the integration of unmanned systems into the commercial ecosystem.
The opinions expressed herein are the author's and not necessarily those of The Maritime Executive.