Interview: Lasse Petterson, President & CEO of Great Lakes Dredge & Dock
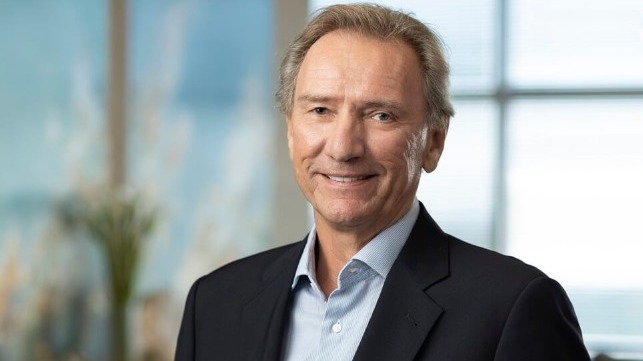
(Article originally published in Sept/Oct 2023 edition.)
Petterson has not only revitalized the U.S.’s biggest dredging company – he’s made it a leader in employee safety and a growing presence in offshore wind.
Let’s start with you – your background and education. What attracted you to the maritime industry?
I’m a U.S. citizen, but I was born in Bergen, Norway and grew up navigating my father’s 22-foot, wooden, one-cylinder diesel-engine boat in the fjords surrounding the town. So love of the sea was in my blood from the beginning. I graduated from the Norwegian University of Technology with a B.S. and then an M.S. in Engineering and was the first in my family to earn a university degree.
During this time the oil fields in the North Sea were being developed, and that’s where I started my career.
Tell us about that. When did you come to the U.S.?
I spent the first nine years of my career at Norwegian Contractors, an offshore oil and gas platform EPC contracting company that was bought by Aker, and then 10 years at Aker Maritime in various executive and operational positions. I came to the U.S. in 1999 as President for Aker, Inc. Since then, I have worked for both U.K. and U.S. oil and gas contracting companies in the U.S. until I was named Chief Executive Officer of GLDD in May 2017. I have served as a member of our Board since December 2016.
GLDD has a long and illustrious history dating back to 1890 and Chicago’s Columbian Exposition. Can you give us a brief overview of that journey and how it became one of the world’s biggest dredging companies?
After building most of the maritime infrastructure in the Great Lakes during our early history, we moved outside the Great Lakes for the first time in 1910 to help deepen Boston Harbor and then New York Harbor and haven’t looked back. Our specialty as the largest dredging company in the U.S. is the larger and more complex projects involving port deepening and coastal rehabilitation as we have built world-class vessels and world-class engineering teams to complete those projects.
Historically, we’ve been instrumental in building and maintaining the U.S. navigation system. We’ve been involved every time a deepening has been required, from 20 feet to 40 feet to 50 feet, and now to 54 feet, so if you’re looking for experience and expertise on soils and environmental conditions in the waterways, come to GLDD. Our diversified organizational knowledge is one of the main assets that sets us apart.
We have people who’ve been dredging for 35–40 years. They know all the ports, all the navigation channels on the East and Gulf Coasts like the back of their hand. So when we’re bidding for new projects, we’re best-positioned to take on those jobs and environments that require complex planning and execution.
How important is the budget of the Army Corps of Engineers for GLDD’s business? Have the federal Infrastructure Investment & Jobs Act and Bipartisan Infrastructure Law also benefited the company?
We have a strong relationship with the Corps, and our success is tied to their success. Their budget has been strong in recent years and, although the IIJA and BIL provided significant funding, we mostly focus on the Corps’ annual appropriations, which need to be robust and consistent to maintain and enhance the nation’s inland waterways. That allows us to build the workforce and equipment capacity needed to meet its needs.
Ironically, although we as well as others in the U.S. dredging industry have been building added dredge capacity in recent years, we’ve found the Corps’ program to be limited and are now starting to rationalize our fleet, including scrapping older dredges, to right-size what we believe is an overbuilt industry at this point.
Does GLDD have an international presence too?
GLDD has worked internationally for over 40 years, and we believe this experience has made us a better company as all of our senior managers have learned how to work in diverse situations. The international projects present special challenges that make us smarter when we do our day-today business in the U.S. and allows us to highlight our world-class safety culture, workforce and fleet. Currently, the international market is down and quite challenging, so we keep a constant eye on other parts of the world looking for opportunities that fit us.
GLDD’s order backlog currently stands at $1.1 billion, a record. Tell us about some of the major projects currently planned or under way. What is the mix between government and private sector work?
We have a good mix of private (LNG) work in Brownsville and Port Arthur, Texas; non-Corps work for port authorities like Houston and the Port of Virginia; and Corps deepening, maintenance and coastal projects and non-Corps coastal projects for clients in North Carolina and Florida. We still have excess capacity and so are pushing for the Corps to continue its improved bidding record in future months and years.
Dredges are truly monster machines, and GLDD has some of the biggest. Tell our readers about the different kinds of dredges. How are they named?
There are three primary types of dredging equipment in the GLDD fleet: cutter suction, trailing suction hopper and mechanical dredges. These are supported by auxiliary vessels and equipment to prepare material for excavation, transport dredged material and power the material through hydraulic pipelines.
Our domestic dredging fleet is deployed continuously around the East and Gulf Coasts and inland rivers. The mobility of the fleet allows the company to respond to changes on demand. We continually assess the challenges and opportunities available. We upgrade and expand our dredging fleet as markets dictate and incorporate the latest and most innovative technologies. We aggressively pursue a program of preventive maintenance, which is reflected in the long life of most of our equipment as well as the low level of unscheduled downtime.
We enjoy naming the vessels, and here tradition applies. We name our hopper dredges after islands, our cutters after states, our multi-cats after capes and, less colorfully, we name our clamshell dredges by number. Our new offshore wind vessel required us to think a bit, and we’ve decided to name these vessels after national parks, taken from an environmentally friendly renewable energy theme, so the first one will be named Acadia!
What other vessels does GLDD own and operate?
Most of our vessels are tied to either dredging or dredging support, so we don’t maintain a fleet that has other purposes. I would like to highlight our new Multi-Cats Cape Hatteras and Cape Canaveral, which have been built solely for the purpose of protecting our workers while working offshore. This gives them a platform to work that is much more stable and safer than what we’ve traditionally required.
Give us an idea of the scope of these operations. How much is a cubic yard of material and how many cubic yards do you typically deal with in dredging and deepening operations? How much does a vessel carry?
As an example, our hopper dredge Ellis Island has a capacity of 15,000 cubic yards, which means it can carry as much as 1,500 truckloads in one load.
The company recently moved from its long-time HQ in Chicago to Houston. What was the strategy behind that, and how many other locations does the company have?
Relocating our corporate offices to Houston from Oak Brook, Illinois puts us closer to key regional customers and new markets, especially along the Gulf Coast and Mississippi River, where we’ve long run major projects and expect to take on additional work.
The relocation also stems in part from changing industry dynamics as the dredging market has shifted from northern Illinois and the Great Lakes to work along the Gulf Coast and Northeast and Southeast coastal regions. The move further allows us to leverage our long-term relationships with the Center for Dredging Studies at Texas A&M University, Louisiana State University and other universities that feature coastal resilience and natural infrastructure initiatives. We do have a regional office in Jacksonville, Florida and in the Middle East.
GLDD was way ahead of the game when it established its Incident and Injury-Free®? (IIF®?) safety program back in 2006. How did that come about, and why is it so important to the company?
We began our IIF®? journey in 2005 with the challenge to transform our company culture from Operations and Safety to SafeOps. IIF®? is now the cornerstone of our organization and drives our ability to perform SafeOps with the mindset of making it personal, relevant and important. Our IIF®? commitment not only guides us in the workplace but also in making safe choices while at home. We’re committed to providing a safe and healthy working environment for all team members and trade partners.
What differentiates GLDD from the competition? What makes it different?
We are a public company and, as such, we need to grow and innovate. Our safety culture is another distinguishing factor that makes us a more professional company. Our track record of success, our size and our willingness to take on the most difficult projects is what makes us different as well.
Two years ago, GLDD established an Offshore Wind sector, which it regards as a “strategic growth area.” Tell us about that and the SRIV currently under construction at Philly Shipyard.
Offshore wind farm developments are coming to the U.S. in a big way. The White House has set a target of 30 gigawatts of offshore wind generation capacity by 2030, which gives us, as an experienced marine company, an excellent opportunity to be at the forefront of new developments.
To capitalize on this opportunity, we signed a contract with Philly Shipyard to build the first U.S.-flagged, Jones Act-compliant subsea rock installation vessel (SRIV) – the Acadia. The vessel will service America’s growing offshore wind industry and is an essential step toward building the marine infrastructure required for this new industry. Signaling the importance of the occasion, President Biden attended the steel-cutting for the Acadia at Philly Shipyard this past July.
Offshore wind will play an important role in the transition to clean energy, and we want to play our part and add to our legacy of environmental responsibility. We have the skillset and talent to give us a big leg-up in this market. Acadia is just the beginning.
The opinions expressed herein are the author's and not necessarily those of The Maritime Executive.