The Evolution of Quantum Marine Stabilizers' Technology and Controls
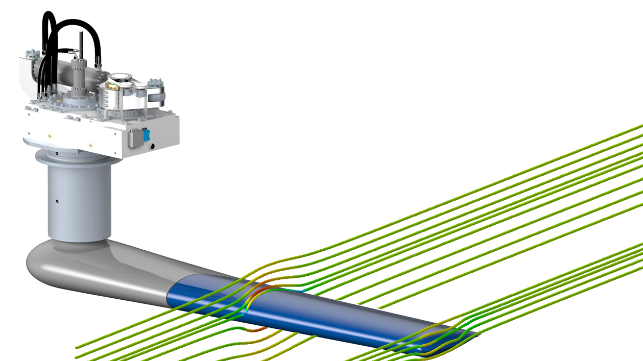
In recent months, Quantum Marine Stabilizers has been developing new technologies involving Windfarm Offshore Service Vessels (OSV) and Next Generation Barge designs. To enhance operational performance even further, Quantum is using artificial intelligence (AI) to predict future wave patterns. Instead of reacting to the existing waves or conditions, the stabilizer systems will analyze the data to make advance corrections with a greater state of readiness, for the waves that will impact the vessel. As the “intelligence” of the controls continue to advance, the applications and benefits include cost savings, safety, ROI and the environment.
Evolution of the Controls
Over the last two decades, there have been incredible advancements to the hydrodynamic design of Quantum’s fins and rotors, but beyond those innovations, the breakthroughs in the control technology has been extraordinary. The controls are the “brains” or proprietary algorithm that automatically senses changes in the ship’s motion and sends adaptive, real-time signals to the stabilizer system. It then uses that data, along with Quantum’s proprietary software, to determine and direct the optimal fin activity to reduce the roll of the vessel. There are many factors that influence the commands or the movement directives, such as wave pattern, roll period, vessel speed, metacentric height (GM), gross tonnage (GT) and hull design/profile.
In order to optimize the roll damping, each stabilizer controller must be configured for the type of system and the intended function:
- Underway and Zero Speed™
- Conventional and XT™ Fins
- MAGLift™ Rotors
- Dyna-Foil™ Retractables
- Pitch Control
Each stabilizer control package includes the following:
- main control and interface
- local control module
- roll sensor
Roll sensor
Main Control and Interface - SMC4000
Early on, the innovation team recognized the importance of digital technology, paving the way for the future. The SMC4000 was designed and engineered with a touch screen panel, HMI (Human Machine Interface) control providing the convenience to integrate with the ship’s “glass bridge.”
SMC4000 – Fin Alarm Status Screen
SMC4000 – Underway Manual Control
An additional HMI can be provided for the EOS (Engineering Operating Space) where any control function of the system can be possible in addition to the bridge control. The “smart,” adaptive logic, tailors the ride, making the SMC4000 ideal for underway and Zero Speed™ applications.
SMC4000 – Mode Selection Screen
If there are two sets of fins, each pair can function independently from the other set. In other words, if there are two sets of fins, one set can be active, while the other pair can be centered or off.
SMC4000 – Rotor Control
The SMC4000 represents significant advancements in system capabilities, options and alerts. Adjusting the parameters and establishing various integrations is greatly simplified, saving time and improving the accuracy. During the commissioning process, the settings for the controls are established and programed.
VPN
When the onboard crew members experience technical challenges, that they are not able to remedy or troubleshoot successfully, they are able to communicate with Quantum’s technicians remotely. With the vessel’s permission, qualified Quantum technicians can run diagnostics through a stabilizer network via a dedicated VPN and resolve the issue promptly.
CFD
The use of CFD (computational fluid dynamics), has enabled Quantum to analyze fin and foil drag characteristics, allowing for optimization of stabilizer shapes to meet or exceed requirements and fuel efficiencies. CFD is a complex study of fluid mechanics and flows that has led to refinements in fin design, advancements in the understanding and prevention of cavitation noise and significant improvements to overall performance (image at top).
Overall Advantages
By reducing seakeeping roll motion at anchor, Quantum’s Zero Speed™ stabilizers allow personnel to perform safer, more efficient, crew, cargo transfer and rescue operations, normally performed at loitering speeds. This allows operators to secure the main engines, decrease fuel consumption and C02 emissions. All Quantum systems are designed to use Environmentally Acceptable Lubricants (EAL) including biodegradable, low toxicity oils and lubricants to protect our fragile ecosystems.
This message is sponsored by Quantum Marine Stabilizers. For more information, please visit quantumstabilizers.com.
The opinions expressed herein are the author's and not necessarily those of The Maritime Executive.