Polymeric Solutions Contributing to Maritime Decarbonization
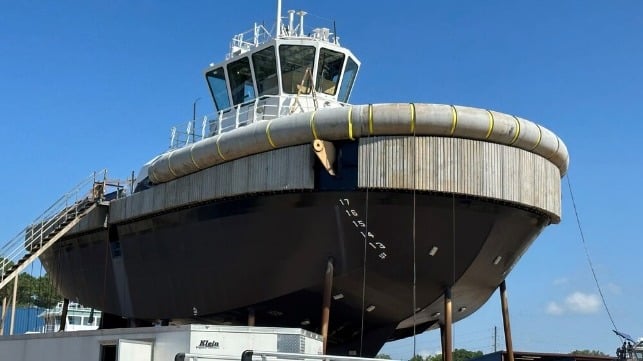
A range of new technologies are emerging to help the maritime sector meet the challenges of decarbonization. Belzona, a designer and manufacturer of polymer repair composites and industrial protective coatings, recently participated in the effort to complete the United States’ first all-electric tugboat, the eWolf. The company provides unique solutions that make repairs possible supporting a circular economic business model that further mitigates carbon emissions.
Meeting the emerging international regulations and the International Maritime Organization’s aspirational goals for reducing carbon emissions will require a tripling of renewable energy capacity and a doubling of energy efficiency improvements by 2030. One of the fundamental ways in which the maritime sector can achieve these goals is through “scalable zero-emission fuels,” and other pioneering technologies. The eWolf, as the U.S.’s first zero-emission tug powered by electricity from its battery system, is a huge step forward in terms of decarbonization.
Launched in 2023, the 82-foot (25-meter) eWolf is leading the way in terms of mitigating the climate impact of the maritime sector. Over the first 10 years of its use, the operation of the new “eTug” will reduce 178 tons of nitrogen oxide (NOx), 2.5 tons of diesel particulate matter, and 3,100 metric tons of carbon dioxide (CO2), versus a conventional tugboat.
The eWolf is capable of speeds of up to 12 knots and will be powered by a 6.2 megawatt-hour main propulsion battery and two electric motors. The electricity comes from a charging station that is part of a microgrid facility, equipped with two energy storage containers. Battery modules in each container have a storage capacity of nearly 1.5 megawatt-hours.
eWolf's forward fender held together with come-alongs during the curing process
Bonding Solution Required for Front Fender
The front fender for the eWolf needed to be bonded together using a strong adhesive that would withstand pushing and pulling forces during the process of adhering the fender to the eTug. Having established confidence in Belzona technology from using their polymeric systems in previous applications, the customer chose Belzona once again for the application.
Following an inspection by Micah Heath, Technical Consultant at Belzona Distributorship, Belzona Alabama, the fast curing, one-part elastomeric primer, Belzona 2911 (Elastomer QD Conditioner), was specified. This conditioner is optimized for adhesion to a variety of substrates including rubber, as required for this particular application. For the bonding, the polyurethane resin, Belzona 2211, was specified. This flexible rubber repair material is optimized for applications where high build, durability, and elasticity are required.
“Once the required surface preparation was completed using grinding wheels and MBX Bristle Blaster, the conditioner, Belzona 2911 (Elastomer QD Conditioner), was applied,” explains Heath. “As soon as the conditioner was touch dry, Belzona 2211 was used to attach the plugs into the fender, and then attach the three-part fender together. The application team used a manual cable puller to apply the necessary pressure to ensure the various surfaces were sufficiently pressed together. Once completed, the application was left for 36 hours to cure, achieving an excellent mechanical bond.”
Fender plugs prior to attachment
Polyurethane resin, Belzona 2211, applied to prepared surface
Contributing to the Circular Economic Business Model
In addition to pioneering technology like the eTug, Belzona highlights that polymeric systems also play a key role in the decarbonization of the maritime sector. Belzona’s circular economic business model is grounded in the practice of repairing and improving damaged assets, rather than decommissioning and replacing them. Not only does this allow the asset owner to make considerable financial savings, but it also mitigates the carbon footprint incurred during the process of replacing damaged assets. In turn, this supports a net zero by 2050 pathway, in line with the Paris Agreement.
In addition, Belzona systems are manufactured according to the ISO 9001 quality management systems and are approved by classification societies from all around the world including Lloyd’s Register, American Bureau of Shipping, Bureau Veritas, RINA Services, DNV, China Classification Society, and the Korean Register of Shipping.
This article is sponsored by Belzona. For more information, please visit: www.Belzona.com
The opinions expressed herein are the author's and not necessarily those of The Maritime Executive.