Digital Innovator is Solving Maritime’s Spare Parts Inventory Problem
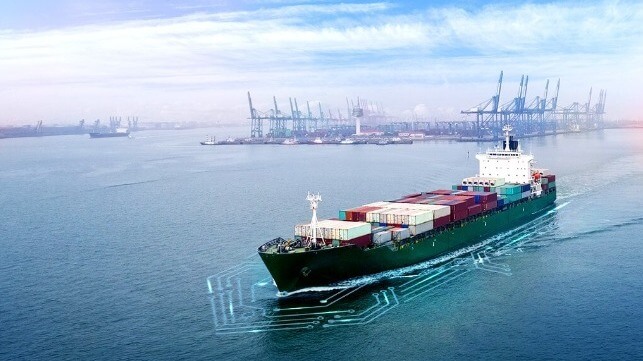
The shipping industry suffers from a lack of accurate data on spare parts storage and consumption. Carrying excess spare parts inventory has historically been an unnecessary cost to the maritime and offshore industry. Fleetwide, an estimated 12 million man-hours go wasted every year to reconcile inventory, only to achieve 20 percent data accuracy. As a result, organizations are continually looking to improve accuracy and optimize operations that cut expenditures.
However, attempts to benefit the whole organization often fail to consider difficult workflow conditions or provide solutions that engineers and staff willingly adopt.
The Solution
Vessel owners and operators require precision clarity on the location of spare parts, inventory levels, and consumption patterns across the fleet. The digitalization of spare parts inventory management delivers increased speed, visibility, and accuracy. More importantly, it provides cost savings. Companies that digitize this process can then better manage cash and activities while reducing human error and operational variance between vessels.
“SparesCNX is bringing spare parts management into the 21st century," says John Slattery, CEO of SparesCNX.
The SparesCNX PROPELLER Internet of Things (IoT) solution enables company-wide visibility throughout the supply chain. PROPELLER can achieve accurate near-real-time spare parts inventory by using Radio Frequency Identification (RFID) and QR-coded tags, artificial intelligence (AI), and machine learning (ML).
The PROPELLER product suite integrates seamlessly with existing planned maintenance systems (PMS)/enterprise resource planning (ERP) platforms and consists of three integrated software and hardware modules:
PROPELLER Ship – Reduces onboard task burden for engineers by utilizing proprietary IoT connected tablets that accurately track RFID- & QR-tagged spare parts inventory. User-centric design and ergonomic products enhance the natural work pace without adding additional labor.
PROPELLER Shore – Aggregates vessel data and uses AI and ML to generate dashboards with actionable insights and procurement recommendations for operational optimization.
PROPELLER Supply – Allows manufacturers, suppliers, and freight forwarders to pre-tag spares and provide shipping status updates along the supply chain.
PROPELLER improves well-being and vessel morale by simplifying onboard and shoreside workflow with tools that are fun and easy to use. Proprietary IoT tablets with integrated cameras and RFID/QR scanners facilitate accurate inventory updating as you go. Total vessel coverage is achieved as inventory can still be completed, even when the tablets are offline. Once back online, data automatically synchronizes with PMS/ERP platforms.
“Crews say the PROPELLER portal and tablet are user-friendly, and it’s like playing with a game on their phone. Finding parts is like using a metal detector that pings the location. Engineers can become fluent with the app in a few hours. Even staff who are reluctant at first appreciate using it. They also love the digital equipment manuals stored on the tablets," says Operations Engineer Ilham Israr.
Key Features of PROPELLER Ship:
- Radar functions help locate misplaced spares,
- RFID/QR tags are linked to Work Orders and Purchase Orders that automatically update ERP,
- Digital equipment manuals stored on the tablet, and
- Optimized stock reconciliation is achieved accurately with a 90 percent efficiency gain.
Captured data from PROPELLER Ship seamlessly feeds to onshore officers, fleet managers, and procurement teams via our highly secure cloud-based PROPELLER Shore portal. The information converts into actionable insights through AI and ML algorithms. Performance data and trends help vessel operators make better business decisions with fleetwide analysis and monitoring of:
- Consumption patterns,
- Procurement cycles,
- Inventory movements,
- Purchase order deliveries,
- Stock Reconciliations,
- Onboard activities, and
- User analytics.
Users can quickly gain highlighted inventory details from the ease of a dashboard, such as critical spares levels, parts that need restocking, purchase orders pending delivery & check-in, and equipment tagging/scanning activity. Different user types, ranging from superintendents, fleet directors, and buyers, can quickly navigate between vessels or business units. Accurate data and visibility provide competitive advantages to make faster and wiser procurement decisions while identifying opportunities for inventory optimization.
Solution Benefits:
- Reduces excess inventory by improving part levels across the entire fleet,
- Benefit from economies of scale by understanding fleet consumption of spares that enable better bulk procurements, &
- Significantly lessen urgent orders through better supply management intelligence.
Recognized for our significant investments and achievements in software solutions that support digitalization for clients, SparesCNX has now partnered with ABS Nautical Systems (ABS NS). The Partnership provides seamless out-of-the-box integration between PROPELLER and ABS NS’ NS Enterprise software suite.
“Our clients are looking for new ways to reduce investment in spare parts inventory and focus those dollars in areas that move their business forward. The PROPELLER platform is a game-changer with intelligent parts management that offers our clients greater capabilities for prioritizing, planning, and supporting these cost reductions," says Evan Gooch, President of ABS Nautical Systems.
The SparesCNX solution uses cutting-edge technology to solve age-old problems. It was developed for seafarers by seafarers and refined through thousands of hours of onboard experience. SparesCNX is progressing the digital transformation process to the commercial maritime fleet.
This post is sponsored by SparesCNX. For more information, please visit www.sparescnx.com or follow them on LinkedIn.
The opinions expressed herein are the author's and not necessarily those of The Maritime Executive.