A New Option for Efficient Low-Speed Propulsion
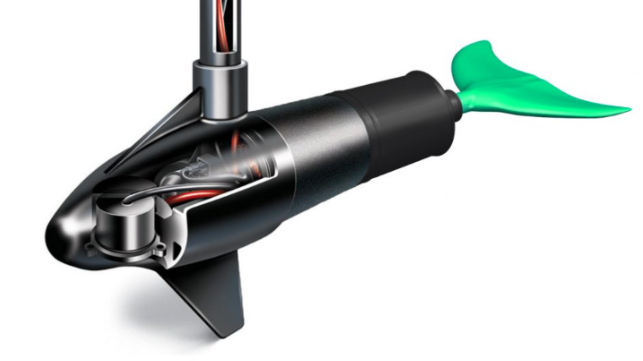
Factors such as rotational speed and the volume flowrate of the water stream compared to sailing speed determine propulsive efficiency of marine propellers, with peak propeller efficiency being achieved in ocean sailing. Speed restrictions imposed on along inland waterways greatly reduce propeller propulsive efficiency. An alternative is evolving in small boat propulsion that offers possible future potential to increase propulsive efficiency of vessels sailing along speed restricted inland waterways.
Introduction
The waterwheel was developed some 4,000-years ago to convert river current to work energy. During the mid-19th century, waterwheels were adapted to provide propulsion as paddle wheels installed on steam powered boats. Propellers evolved from windmills and enhanced directional control compared to stern wheel and side wheel propulsion when vessels sailed through waves. The biggest propellers installed at the stern of large commercial vessels deliver the highest propulsive efficiency, at certain sailing speeds. Until recently, there was little interest in adapting a radically different technology to vessel propulsion, but this has changed with the appearance of hydrofoil surfboards.
Hydrofoils configured like scale-model airplanes were originally installed under surfboards to improve surfing through choppy water. Surfers learned to “pump” the hydrofoil surfboards to achieve propulsion after a wave dissipated and also to travel across “flat water," the pumping producing whale or dolphin-like movement of the rigid hydrofoil tail wing. A Swedish company called DOL-prop Industries has developed a competing propulsion technology for small vessels, based on the tail fluke of whales and dolphins. They claim to have eliminated cavitation and offer superior propulsive efficiency than conventional propellers used on small boats.
Competing Concepts
While hydrofoil surfboard tail wings are rigid, the Swedish fluke propulsion technology duplicates the characteristics of a dolphin’s tail fluke in that it is soft and flexible. The South African built “pump-a-bike” was a human-powered hydrofoil that combined a small leading hydrofoil and a wide trailing hydrofoil on a transverse shaft placed below the rider. After push the bike from a dock, the rider hopped aboard and then jumped up and down above the rear hydrofoil to achieve propulsion. At the present day, hydrofoil surfboards represent the main widespread use of propulsion without the propeller.
A version of the South African pumping-hydrofoil concept was installed at the bow of a wave-powered boat, where a floating device connected by control rods raised and lowered the propulsion hydrofoil to propel the vessel to a speed of 6-knots. While the technology showed promise, market acceptance of powered fluke propulsion on small vessels has been quite low despite improved efficiency. The commercial maritime sector would likely wait to see widespread operation of powered fluke propulsion on small vessels before developing a ship size version of the technology, for use along speed restricted inland waterways.
Large Vessel Application:
Large commercial-size vessels propelled by fluke propulsion would require bow and stern thrusters to optimize directional control. Such vessels built for operation along inland waterways could carry grid-scale electric battery storage technology such as long-life flow redox batteries or competing liquid metal storage battery technology. There would be opportunity to do partial recharging when the vessels transit across navigation locks. The potentially higher propulsive efficiency of fluke technology over propellers used on vessels that sail along speed restricted waterways would likely and significantly increase sailing distance before onboard batteries require recharging.
During an earlier period, there was little pressure on the commercial maritime sector to reduce carbon emissions. At the present time, the European Community seeks to impose increasingly more stringent standards on ship exhaust emissions. The shipping industry has responded by switching some ships to LNG fuel with future options involving hydrogen fuel cell technology. Such power generation technology is also being installed on vessels that operate along inland waterways, where large-scale versions of specially developed fluke propulsion technology could be retrofitted to the stern areas of a few vessels powered by battery or by fuel cell energy technology.
Crank Activated Fluke
It appears possible that a crankshaft driving a connecting rod could activate the spring-loaded Swedish DOL-prop fluke propulsion technology, perhaps with an electric motor or wind turbine driving the crankshaft. Spring loading a large-scale rigid or non-flexible giant fluke would be impractical and require a different form of activation, to raise and lower the fluke while changing its angle away from the horizontal to produce thrust. One possible option would involve the combination of forward and rear transversely mounted crankshafts driving forward and rear connecting rods attached to the forward and rear areas of the fluke.
The combination of long-stroke forward and shorter-stroke rear transverse crankshafts might be independently driven by different electric motors, with potential to connect the pair of crankshafts using side-rods with the forward and rear crankshafts set out of phase to produce forward thrust. A pivoted mechanical link would connect the fluke’s leading end to the boat stern area, with the option of pivoted upper and lower links changing fluke angle as it rises and falls when activated by a single crank. Alternatives involving large-scale rigid fluke vertical activation and pitching would be subject to future research.
Wind Power
This era is witnessing renewed interest in wind-powered vessels that include windmill powered boats capable of sailing at eight knots directly into a headwind, using a conventional propeller and three-bladed turbine. For small vessels, the dolphin fluke DOL-prop offers a significant gain in propulsive efficiency over small propellers. A unique wind turbine developed in California offers higher power output for the same diameter as a three-bladed turbine. It is a twin-rotor turbine using a pair of two-bladed turbines set at 90-degrees to each other and a distance between each other on the same power shaft.
A competing technology involved a power generation kite attached to the vessel stern and able to “pump” the DOL-prop power level to produce propulsion. Wind propelled vessels using fluke propulsion and could sail directly into headwinds along many inland waterways internationally, carrying cargo to market. Mechanical stresses caused by vessel pitching and rolling restrict the height of wind turbine tower, and the size of the wind turbine that the tower could carry. Nevertheless, the combination of efficient and innovation wind power conversion technology and fluke propulsion promises to be potentially competitive in future carbon-free vessel propulsion.
Conclusions
A maritime industry that seeks to reduce ship exhaust emissions and improve propulsive efficiency may wish to examine the potential of mechanical fluke propulsion applied to small and large vessels. A large-scale mechanical fluke activated by a pair of crankshafts offers potential to improve propulsive efficiency along inland waterways.
Harry Valentine is a regular contributor to The Maritime Executive.
The opinions expressed herein are the author's and not necessarily those of The Maritime Executive.