Designs for a Panamax CO2 Gas Carrier to Support CCUS Projects
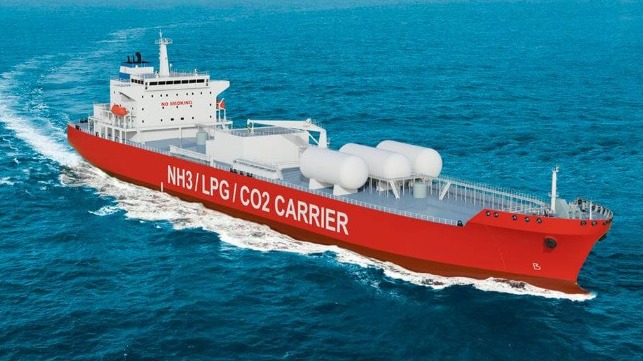
Carbon Capture Utilization and Storage (CCUS) is considered to be one of the most promising technologies, especially for large-scale industries that will be difficult to decarbonize. However, there needs to be large and economical solutions for the transportation of CO2 to achieve sustainable CCUS projects.
Exmar, a gas carrier operator headquartered in Belgium, is partnering with Lattice, a South Korean tank manufacturer, to develop a new type of CO2 carrier that they believe will provide the solutions required to transport large quantities of carbon for either reuse in industrial applications or storage. They join others in the shipping and shipbuilding industry that are also working on designs for a new generation of gas carriers suited to CO2 transportation.
The two companies are forming a joint venture to develop and design a large-scale gas carrier using the companies’ experience in the design, ownership, and operation of gas carriers and tank design. They reported that a preliminary study shows that Lattice’s Pressure Vessel tank design is well suited to providing solutions for large-scale CO2 transportation at low and medium pressures.
Their initial concept is for a 640-foot-long Panamax beam vessel with a cargo capacity of 40,500 m3. Such a vessel would be tailored to support CCUS projects with capacities ranging from 2 to 10 MTPA. Additionally, they also plan to provide a 3,000 m3 storage capacity for low CO2 emitting fuels like LPG Ammonia or LNG.
“The design and vessel size can be adjusted to meet all required transport volumes to ensure the most optimal logistical solution in the most cost-competitive way,” the companies said in announcing their joint venture. It will also be suitable for LPG and Ammonia transportation.
In addition, the tank design will also provide a storage solution for offshore CO2 liquefaction or re-injection projects. The pressurized storage tanks they said can be made in an efficient shape fitting the ship hull and allowing for large storage capacity. An additional benefit for offshore storage is that the tank design prevents sloshing problems even in the harshest environments.
Several other projects are also underway in the industry developing CO2 carriers. In Japan, Mitsubishi Shipbuilding is working with French oil major TotalEnergies on opportunities to build large LCO2 carriers. South Korean steel company POSCO is also working in conduction with Korea Shipbuilding & Offshore and the Hyundai Mipo shipyard owned by KSOE, with Lloyd’s as its class society, for designs focusing on the tanks required to transport CO2. ABS has partnered with South Korean shipbuilder Daewoo Shipbuilding & Marine Engineering (DSME) to develop designs for a 70,000 cubic meter very large liquefied CO2 carrier, while Wärtsilä Gas Solutions reported that it received an AiP for a cargo containment system to be used on a liquid CO2 carrier.